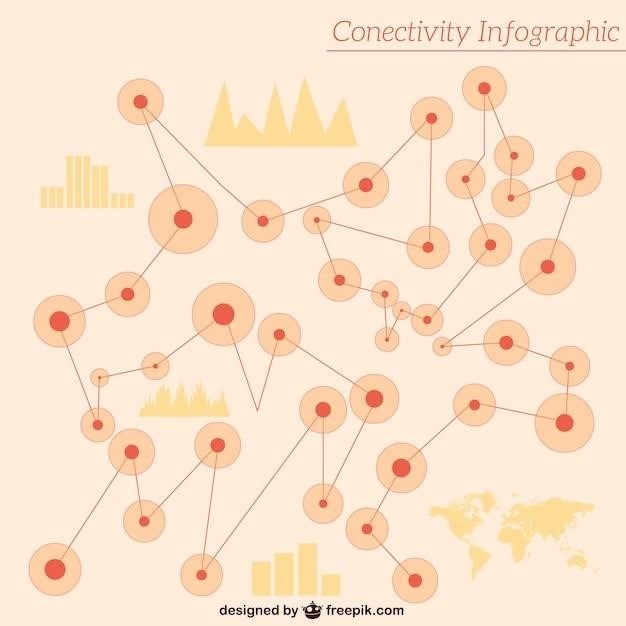
Unified Fine Threads (UNF)
UNF threads are unified fine pitch threads. They are a standard type of screw thread used in a variety of applications. UNF threads have a smaller pitch than UNC threads, which means that they have more threads per inch. This makes them stronger and more resistant to loosening. UNF threads are also more accurate, which makes them ideal for applications where precision is important.
Introduction
The world of mechanical engineering relies heavily on standardized components for efficient design and manufacturing. Among these standards, screw threads play a critical role in securing and joining parts, ensuring proper functionality and longevity. Unified National Coarse (UNC) and Unified National Fine (UNF) threads are two prominent thread series used in the United States and internationally, each serving distinct purposes. A comprehensive understanding of these threads is crucial for engineers, machinists, and anyone involved in assembling or designing threaded components.
The UNC and UNF thread chart, often presented as a PDF document, serves as a valuable resource for quick reference and accurate selection of thread sizes. This chart organizes thread specifications, including diameter, pitch, and thread per inch (TPI), allowing users to easily identify the appropriate thread for their application. Whether designing a complex machine or a simple assembly, the UNC/UNF thread chart is an indispensable tool for ensuring proper fit, strength, and compatibility.
This article aims to provide a detailed overview of the UNC and UNF thread chart, explaining its structure, key elements, and practical applications. We will explore the advantages and limitations of each thread series, highlighting the factors that guide the selection process. By understanding the information contained in the chart, users can make informed decisions about thread selection, ensuring the success of their projects.
What are UNF Threads?
Unified National Fine (UNF) threads are a standard type of screw thread used in various applications where precision, strength, and resistance to loosening are paramount. They are distinguished by their fine pitch, meaning they have more threads per inch compared to their counterpart, the Unified National Coarse (UNC) thread. This finer pitch offers several advantages, making UNF threads suitable for applications where precise adjustments and tighter tolerances are required.
The UNF thread standard is defined by the American Society of Mechanical Engineers (ASME) and the American National Standards Institute (ANSI) in the United States, ensuring consistent and reliable thread specifications. The UNF thread series includes a range of sizes, each identified by its nominal diameter and threads per inch. For instance, a 1/2-20 UNF thread indicates a thread with a 1/2-inch nominal diameter and 20 threads per inch.
UNF threads are commonly found in applications where vibration, shock, or frequent adjustments are anticipated. Their increased thread density provides greater resistance to loosening under these conditions. Furthermore, the finer pitch enables tighter fits, reducing the likelihood of thread stripping or galling during assembly or disassembly. UNF threads are also preferred in applications where strength is a critical factor, as the larger thread engagement area allows for higher clamping forces.
Advantages of UNF Threads
UNF threads offer several advantages over their coarser counterparts, making them suitable for a wide range of applications where precision, strength, and durability are essential. The finer pitch of UNF threads results in a greater number of threads per inch, leading to enhanced performance and reliability in various scenarios.
One of the key advantages of UNF threads is their superior resistance to loosening. The increased thread engagement area provided by the finer pitch creates a tighter fit, minimizing the risk of threads backing out due to vibration, shock, or repeated assembly and disassembly. This is particularly crucial in applications where components are subjected to significant dynamic forces or where maintaining a secure connection over time is paramount.
Another significant advantage of UNF threads is their enhanced strength. The finer pitch allows for a larger stress area, enabling the thread to withstand greater tensile and shear loads. This increased strength is particularly beneficial in applications where the threaded connection is subjected to high forces or where the integrity of the connection is critical to the overall system’s performance.
Moreover, the smaller helix angle associated with UNF threads facilitates smoother engagement and reduces the likelihood of thread stripping or galling during assembly or disassembly. This attribute is particularly important in applications where frequent adjustments are required or where the use of high-strength materials could lead to increased friction and wear on the threads.
UNF Thread Sizes and Specifications
UNF thread sizes are defined by their nominal diameter and the number of threads per inch (TPI). The standard for UNF threads is ANSI/ASME B1.1⁚2003. This standard outlines the dimensions, tolerances, and other specifications for UNF threads. The thread designation is typically expressed as “UNF” followed by the nominal diameter and TPI, for example, 1/2-20 UNF. This indicates a thread with a nominal diameter of 1/2 inch and 20 threads per inch. The standard also specifies the pitch diameter, minor diameter, and other critical dimensions for each thread size.
UNF threads are available in a wide range of sizes, from very small diameters used in miniature applications to larger diameters employed in heavy-duty machinery. The specific thread sizes and their corresponding specifications are often presented in a tabular format known as a thread chart. These charts provide a comprehensive reference for engineers, machinists, and other professionals who require accurate information about UNF thread dimensions and tolerances.
Thread charts typically include information such as the nominal diameter, pitch, thread pitch diameter, minor diameter, thread depth, thread angle, and the corresponding tap drill size for each thread size. This information is essential for selecting the appropriate tap and die for threading a specific component and ensuring proper thread engagement and fit. UNF thread charts are available in various formats, including printed documents, online databases, and software programs, making this valuable information readily accessible to those who require it.
UNF Thread Chart PDF
A UNF Thread Chart PDF is a digital document that presents a comprehensive table of Unified National Fine (UNF) thread specifications. This chart is an invaluable resource for engineers, machinists, and anyone involved in the design, manufacturing, or assembly of threaded components. It provides a clear and organized format for accessing essential information about UNF thread sizes and their corresponding dimensions.
A typical UNF Thread Chart PDF includes columns for various parameters, such as the nominal diameter of the thread (in inches), the number of threads per inch (TPI), the thread pitch (the distance between two adjacent threads), the major diameter (the largest diameter of the thread), the minor diameter (the smallest diameter of the thread), and the thread pitch diameter (the average diameter of the thread). These charts may also include additional information, such as the tap drill size, thread tolerance, and thread engagement length.
UNF Thread Chart PDFs are readily available online from various sources, including manufacturers of fasteners, engineering software providers, and educational institutions. They can be downloaded and printed for easy reference or saved electronically for convenient access. These charts are an essential tool for ensuring that the correct UNF thread is selected for a specific application, guaranteeing proper fit and function of threaded components.
Applications of UNF Threads
UNF threads find widespread use in a variety of industries and applications due to their strength, precision, and resistance to loosening. Their fine pitch and increased thread engagement contribute to their suitability for situations demanding high tensile strength, accurate alignment, and reliable fastening.
In the automotive industry, UNF threads are commonly used for engine components, suspension systems, and other critical areas where vibration and stress are significant factors. Their fine pitch and increased thread engagement help ensure that bolts and nuts remain securely fastened even under extreme conditions.
UNF threads are also frequently used in aerospace applications, where weight reduction and high reliability are paramount. Their strength and precision make them ideal for securing components in aircraft and spacecraft structures, ensuring that they can withstand the rigors of flight and space travel.
Other industries that utilize UNF threads include manufacturing, construction, and electronics. They are used in a wide range of applications, from industrial machinery and heavy-duty equipment to delicate electronic components and precision instruments. Their versatility and reliability make them a popular choice for a wide range of fastening needs.
UNF Thread Standards and Regulations
UNF threads are governed by a set of standards and regulations that ensure consistency and compatibility across different manufacturers and applications. These standards specify the dimensions, tolerances, and other critical characteristics of UNF threads, ensuring that parts from different sources can be interchanged reliably.
The primary standard for UNF threads is ANSI/ASME B1.1, which outlines the specifications for unified inch screw threads. This standard covers a wide range of thread sizes, pitches, and classes, providing a comprehensive framework for UNF thread design and manufacturing.
In addition to ANSI/ASME B1.1, other standards and regulations may apply depending on the specific application or industry. For example, the aerospace industry has its own standards for UNF threads, which are designed to meet the stringent requirements of aircraft and spacecraft applications.
Adherence to these standards and regulations is crucial for ensuring the quality, reliability, and safety of products that utilize UNF threads. They provide a common language and framework for thread design, manufacturing, and inspection, facilitating the development and use of interchangeable parts across different industries and applications.
UNF Thread Design Considerations
Designing with UNF threads involves a careful consideration of several factors to ensure optimal performance and reliability. These factors include the specific application, the required strength and load capacity, the desired level of precision, and the materials being used.
One key consideration is the selection of the appropriate thread size and pitch. A larger thread size provides greater strength and load capacity, but also requires a larger hole and may be less suitable for applications where space is limited. A finer pitch, as found in UNF threads, offers greater precision and finer adjustments, making it ideal for applications where precise positioning or fine-tuning is crucial.
The material choice plays a significant role in the strength and durability of the threaded connection. Stainless steel is often preferred for its corrosion resistance, while other materials like brass or aluminum may be suitable for specific applications depending on factors like weight and cost.
Furthermore, the design should account for the potential for stress concentrations around the thread root and crest. This can be mitigated by utilizing appropriate thread form and ensuring sufficient material thickness around the thread. Proper design considerations can minimize the risk of thread failure under load.
UNF Thread Manufacturing
The manufacturing of UNF threads involves a precise process that ensures consistent quality and dimensional accuracy. Several methods are employed for creating UNF threads, each with its own advantages and limitations.
One common method is thread rolling, which involves using a pair of hardened steel dies to deform the material and create the thread profile. This process is highly efficient and produces threads with excellent surface finish and strength; However, it is suitable for relatively soft materials and limited in terms of thread size and complexity.
Another method is thread cutting, which involves using a cutting tool, such as a tap or die, to remove material from the workpiece and create the thread. This method offers greater flexibility in terms of thread size and material, but it can lead to burrs or uneven thread profiles if not performed correctly.
For more complex or high-precision threads, CNC machining is often employed. This method uses computer-controlled tools to precisely cut the thread profile, ensuring accuracy and repeatability. CNC machining can produce intricate threads in a variety of materials but is more expensive and time-consuming than other methods.
Regardless of the method used, the manufacturing process for UNF threads must adhere to strict quality control standards to ensure that the threads meet the required specifications for pitch, diameter, and surface finish. This ensures that the threads will function correctly and provide the desired strength and performance.
UNF Thread Inspection and Testing
Ensuring the quality and reliability of UNF threads is crucial for their intended applications. This requires rigorous inspection and testing procedures throughout the manufacturing process. Several methods are employed to assess the conformity of UNF threads to specified standards and ensure they meet the required performance criteria.
Visual inspection is often the first step, where trained inspectors examine the threads for any defects or inconsistencies. This includes checking for burrs, scratches, and other surface imperfections that could compromise thread integrity. Microscopic examination may be used to detect subtle defects not visible to the naked eye.
Dimensional measurements are vital to ensure that the thread pitch, diameter, and other critical dimensions conform to the specifications outlined in relevant standards. This typically involves using precision measuring instruments like calipers, micrometers, or thread gauges.
Functional testing assesses the thread’s ability to perform as intended. This may involve measuring thread engagement and torque requirements, as well as evaluating the thread’s resistance to stripping or failure under various loading conditions.
Material testing is also essential to verify the thread’s strength and resistance to corrosion. This may involve analyzing the material’s chemical composition, tensile strength, and hardness.
By implementing these rigorous inspection and testing procedures, manufacturers can ensure that UNF threads meet the highest quality standards and provide reliable performance in their applications. This is essential for ensuring the safety and functionality of products relying on UNF threads for assembly and fastening.
UNF Thread Resources
For those seeking comprehensive information and resources on UNF threads, a wealth of knowledge is readily available online and in published materials. These resources provide valuable insights into the intricacies of UNF threads, their applications, and the standards governing their design and manufacture.
The American Society of Mechanical Engineers (ASME) offers a comprehensive standard, ANSI/ASME B1.1, which outlines the specifications for Unified Inch Screw Threads, including UNF threads. This standard provides detailed information on thread dimensions, tolerances, and other critical parameters.
Numerous online platforms and websites dedicated to engineering and manufacturing provide valuable information on UNF threads, including thread charts, calculators, and conversion tables. These resources can assist in selecting the appropriate UNF thread size for specific applications and aid in calculating thread engagement and torque requirements.
Published books and technical journals on engineering and manufacturing also offer in-depth coverage of UNF threads, including their history, design principles, and applications. These resources provide a more comprehensive understanding of the subject, delving into the theoretical aspects of UNF threads and their role in various engineering disciplines.
By exploring these resources, individuals can gain a comprehensive understanding of UNF threads, ensuring they make informed decisions when selecting and using them in their projects and applications.
UNF threads, a crucial component in various engineering applications, offer distinct advantages over coarse threads. Their finer pitch provides greater strength, precision, and resistance to loosening, making them ideal for applications demanding close tolerances and high load-bearing capacity. The widespread use of UNF threads across diverse industries highlights their versatility and reliability.
Understanding the intricacies of UNF threads, their specifications, and their applications is crucial for engineers, designers, and manufacturers. The availability of comprehensive resources, including UNF thread charts, standards, and technical literature, facilitates informed decision-making and ensures the successful implementation of these threads in various projects.
As technology continues to evolve, the demand for accurate and reliable fasteners is expected to increase. UNF threads, with their inherent strengths and precision, are poised to play a vital role in meeting these demands. Continued research and development in the field of thread design and manufacturing will further enhance the capabilities and applications of UNF threads.
In conclusion, UNF threads represent a vital aspect of modern engineering and manufacturing. Their versatility, strength, and precision make them a cornerstone in various applications. The wealth of resources available provides ample support for engineers and designers in selecting and implementing these threads effectively, ensuring successful outcomes in diverse projects.
No comment yet, add your voice below!